When implementing ISO 9001:2015, many organizations worry about documentation. I understand this concern. However, the revised standard offers flexibility. It lets organizations decide the right amount of documented information to show effective planning, operation, and process control. This makes it easier for companies of all sizes to align with the standard without unnecessary paperwork.
What is Requirements Engineering?
Requirements engineering involves defining, documenting, and managing requirements for products or services. It ensures the end result meets stakeholder needs. By carefully gathering and analyzing requirements, I can lay the foundation for a successful quality management system (QMS).
What Is Requirements Documentation?
Ever started a project only to realize halfway through that people had wildly different ideas of what success looks like? That’s where requirements documentation comes in. It’s the backbone of any successful project, laying out what needs to be built, why, and how it should work — all in clear, structured detail.
By capturing stakeholder expectations, technical constraints, and key functionalities, this document keeps everyone aligned. It reduces misunderstandings, prevents scope creep, and saves countless hours of rework. Whether you’re developing software, designing a system, or rolling out a new service, solid requirements documentation bridges the gap between vision and reality.
Understanding Documented Information in ISO 9001:2015
The term “documented information” replaces previous concepts like procedures, records, and manuals. This change emphasizes results over rigid documentation structures. According to ISO 9001:2015, documented information serves three main purposes:
- Communication: Documents transmit knowledge across the organization. Depending on the company’s size and complexity, this could range from formal reports to simple checklists.
- Evidence of Conformity: Documentation proves processes were carried out as planned. This might include test results, inspection records, or meeting notes.
- Knowledge Sharing: Documents preserve organizational knowledge. For example, technical specifications help guide future product development.
ISO 9001:2015 doesn’t dictate the format of documentation. It allows organizations to choose what works best for them. Whether it’s a digital file, a physical manual, or even a master sample, the key is to maintain control over the information.
Documentation Requirements in ISO 9001:2015
Clause 4.4 requires maintaining documented information to support process operations. It also requires retaining information as evidence that processes meet expectations. Meanwhile, Clause 7.5 details how to manage documented information. This includes creating, updating, and controlling documents.
The extent of documentation varies depending on factors like:
- Organization size and complexity
- Process interactions
- Employee competence
For smaller, simpler organizations, minimal documentation might suffice. Larger, more complex organizations may need more detailed records.
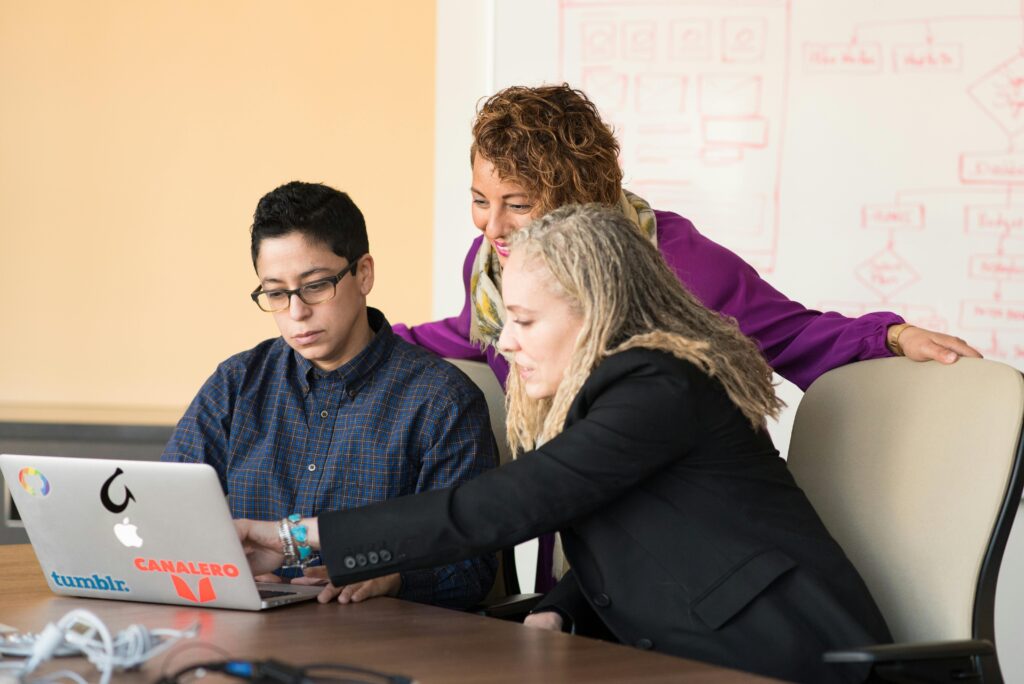
Types of Documented Information
ISO 9001:2015 outlines three categories of documented information:
- High-level documents: These establish the QMS framework. Examples include the quality policy, objectives, and process descriptions.
- Operational documents: These guide day-to-day activities. Examples include work instructions, production schedules, and test plans.
- Records: These provide evidence of outcomes. Examples include calibration logs, audit results, and nonconformity reports.
Each type serves a distinct purpose, but all contribute to an effective QMS.
Implementing a Quality Management System (QM 6S)
When starting a QMS, I recommend focusing on processes first. Understand what needs to happen, then decide how much documentation is necessary. For instance, documenting a complex production process might prevent costly errors, while over-documenting a simple task could waste resources.
For organizations with existing QMSs, transitioning to ISO 9001:2015 offers an opportunity to streamline documentation. I often suggest consolidating redundant documents and eliminating unnecessary ones. The goal is to keep what adds value and discard what doesn’t.
Demonstrating Conformity with ISO 9001:2015
Organizations can prove compliance without excessive paperwork. The key lies in objective evidence — data supporting process effectiveness. While some clauses specifically require records, many allow flexibility. For example, Clause 8.1(e) leaves it to the organization to decide what documentation proves effective planning and control.
I always advise organizations to strike a balance. Document enough to show conformity and ensure process stability, but not so much that documentation becomes a burden.
Final Thoughts
ISO 9001:2015 aims to simplify quality management. It replaces rigid documentation rules with flexible, results-oriented requirements. This allows organizations to tailor documentation to their needs, fostering both compliance and efficiency. Whether starting from scratch or updating an existing QMS, I encourage organizations to view documentation as a tool — not a hurdle. When used wisely, documented information supports continual improvement and long-term success.
Disclaimer: The content of this article aims to provide an initial understanding of the topic and does not replace technical, legal or business procedural advice and guidance.
Credits: Photo by Christina Morillo from Pexels